UE Manufacturing Services
Maintenance & Repair
UEM has a service team of individuals specializing in the maintenance and repair of our equipment. Our warranty policy on equipment is valid for 12 months from delivery. This is in conjunction with any manufacturer warranty that may apply.
Our service team will commonly travel to location upon request and perform repair work on-site. Outside of warranty work, our guys are often called out to perform work on a customer unit that is due for PM’s (preventative maintenance), among other things.
Our service trucks travel across the country to provide the same great service that we offer right in our Oklahoma City manufacturing plants. Our team of service technicians combine together a vast amount of experience in the oilfield industry and are always available on call.
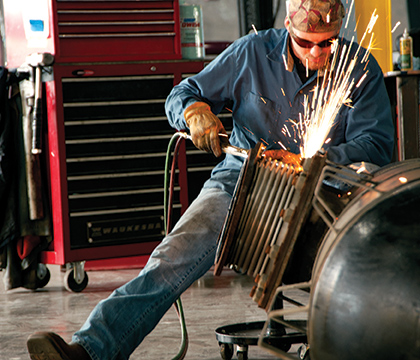

Oilfield Equipment Training
We always offer an additional equipment training service with the delivery of a completed unit that can be performed for the customer at their place of business. This service is offered globally to train the new operators on how to run and maintain the machinery.
We are also able to provide this service at either of our two Oklahoma City test facilities. Just as the unit is tested per customer specific requirements before delivery, the same facility can offer training to individuals who will be operating the equipment in the field.
Equipment Testing Facility
At UEM, it is standard that the products we put out into the field are performing at the highest of levels. One of the key aspects in achieving this is our rigorous final CAT (Customer Acceptance Test) testing that takes place at one of our three test facilities.
We will put each of our completed units through multiple simulated field endurance tests that will give us the ability and confidence knowing the unit will stand up to the demand expected of it. The customer always has an open invitation to attend this testing should they wish to do so.
Between our three testing facilities we are capable of testing anything from a blender to a nitrogen pump. Our test stands are equipped with Endress Hauser and cRio recording software and dozens of channels which allow us to record in real time pertinent pressures and temperatures any given unit.
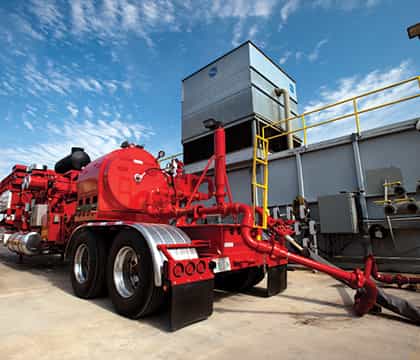
As we prepare a unit for testing, we will be gathering important information from serial numbers on components to certification bands on high pressure iron. Once a unit has been pressure tested and considered safe, depending on what that particular customer requires, testing will begin.
With respect to the different requirements of our testing, each unit will be carefully watched and monitored with a final package of all the data collected being delivered with the unit upon completion. An average test will take approximately 6-8 hours minimum.